WAREHOUSE PROCESSES SUPPORT
Linker's OMS:
benefit from packaging video recording
Take full control of your e-commerce packaging preparation and shorten the turnaround time to literally few seconds:
- Quick and easy access to the specific packaging process record;
- Reduction in the total number of shipment complaints by more than 50%;
- 100% effective handling of complaints - complete monitoring of the packaging process and provision of irrefutable evidence to the end customer!
.png)
800
k
orders handled
monthly
>5
years
industry experience
99
%
SLA Support
+5
mln
operations handled
monthly
>30
%
of logistics costs optimization
.png)
PROFIT FROM COMPETITIVE ADVANTAGE
Comprehensive claim handling
Customers have the right to complain if products are faulty, do not match the description or if the products sent do not match the order specifications.
Complaint handling from the point of view of the shop can be difficult and time-consuming, but good complaint handling always contributes to increased customer loyalty and a positive image for the online shop.
Therefore, it is important that the complaints process is fast, efficient, and customer-friendly.
WAREHOUSE PERSPECTIVE
Challenges in the reclamation process
If the warehouse does not have clear procedures for handling complaints, it can be difficult for staff to resolve customer issues quickly and effectively. This can lead to delays in handling complaints and dissatisfied customers.
2. insufficient knowledge of product characteristicsStore employees need to have a good knowledge of the products sold by the online shop to fully understand the customer's problem and offer an appropriate solution. Lack of staff knowledge can lead to wrong decisions and dissatisfied customers.
3. The need to collect evidenceUnfair customer practices unfortunately still happen and without hard evidence, they are often a stock cost. To successfully reject a complaint, we need evidence to do so with a clear conscience. That is why we often have CCTV footage captured by a camera placed at the e-commerce parcel packing station.
When an order shortage is reported, the most common verification path is to check stock levels. To do this, we instruct a warehouse employee to count all the products we have in stock to verify if the claim is valid. If we are recording the process in CCTV - it is necessary to extract information from the system about where and when the package was packed. It is necessary to find a specific piece of footage in a roll of footage from the entire warehouse, which can often be a time-consuming challenge.
5. Information flow
Throughout the claims process, we often have a lot of information chaos. Assuming a scenario with outsourcing logistics to an operator, we have as many as 4 entities: Notifier, Seller's Contact Centre, Customer Service at the Operator, and Warehouse. The flow of information itself can be very problematic and time-consuming. In the end, it translates into the shoppers' in-store experience and their relationship with the brand.
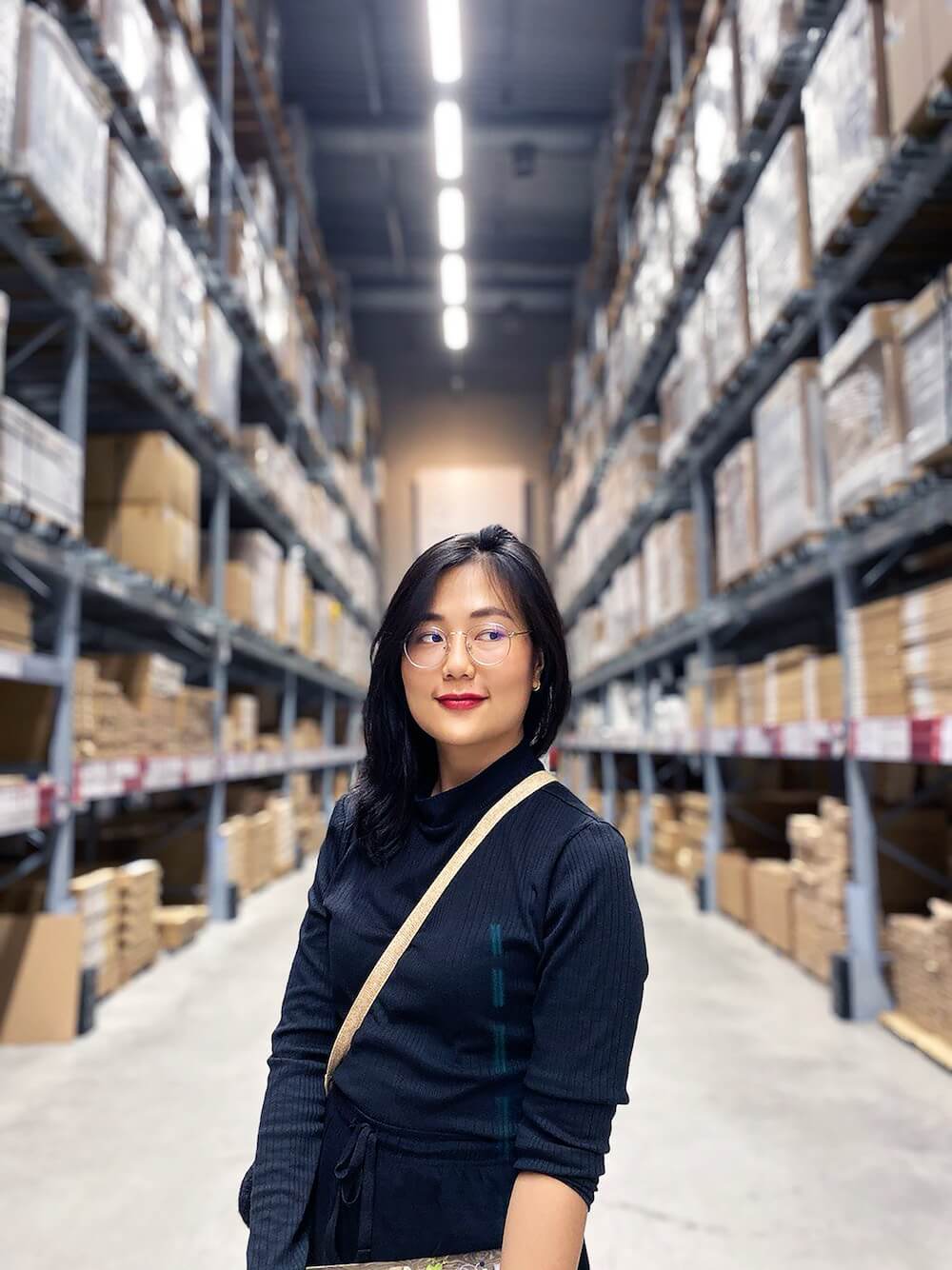
ONE TOOL, MULTIPLY SAVINGSS
Notably shortened verification process
Together with our partner, we verified the time it takes to verify complaints on the warehouse side.
The average exceeds more than one hour over each individual complaint, taking into account activities such as:
- Acceptance of notification
- Verification of order
- Preparation of packing station data and start and end dates and times
- Searching for the recording on CCTV
- Cutting and export of the recording
- Reply to responsible person
Normally, such a process drags on for several days, sometimes even for several weeks. With Linker Cloud, it takes less one hour!
DETAILED EXPLANATION
How it works:
-1.png?width=1200&height=509&name=Untitled%20design%20(5)-1.png)
EQUIPMENT
We offer assistance in the selection and purchase of appropriate equipment (cameras, DVRs, servers, etc.) along with support for the installation of cameras at packing stations
SOFTWARE
We provide the software that controls the cameras. We start recording with the start of packaging end we end recording when the shipment is closed and labeled
RECORD
Access to the recording is from the order level where you will find a photo of each packed package. Each recording is tagged with the product information that was, scanned during packaging, allowing you to instantly get to the part of the recording you need.
SELECTED OMS CLIENTS
Trusted by industry leaders:
.png)